CMT
Este método de unión moderna satisface las exigencias cada vez más estrictas,. algunos de los más importantes de los cuales son la estabilidad del proceso, la reproducibilidad y la relación coste-eficacia.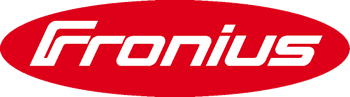
Queres descubrir el nuevo proceso CMT de Fronius?
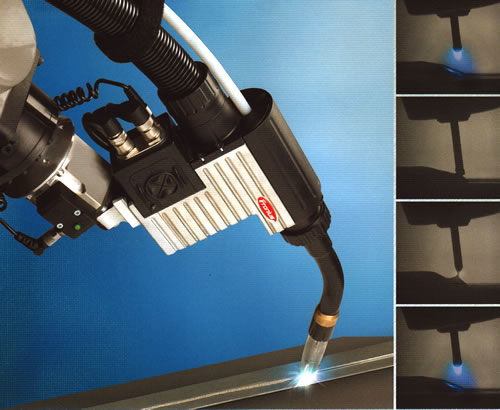
Aplicación y ventajas
La aplicación estrella del proceso CMT es ciertamente la unión de acero con aluminio. A pesar de que el material base de acero en esta soldadura sin fusión no se derrite, sino que sólo se moja, numerosas pruebas de tensión muestran siempre un quiebre en el material base de aluminio y no en el cordón de soldadura.
Además del ensamble de acero con aluminio, el proceso CMT ha demostrado ser también idóneo para muchas otras aplicaciones. Sin duda hay una gran demanda para la soldadura sin fusión prácticamente libre de salpicaduras, de láminas galvanizadas a fuego y por electrólisis, con un alambre de soldadura con aleación de cobre-silicio. Se han realizado experimentos concretos para la fusión de láminas galvanizadas (0.8 mm) y material negro (5 mm), con una distorsión extremadamente pequeña de la lámina galvanizada.
También la soldadura de láminas delgadas (0.3 – 0.8 mm) de chapa de aluminio es posible. En éstas, la baja transferencia térmica del proceso CMT permite dejar de utilizar un baño de fusión, sin el riesgo de que el cordón de soldadura se rompa. Lo mismo sucede también con la soldadura de aceros inoxidables y con el magnesio.
Tecnología del Dispositivo
La soldadura CMT funciona exclusivamente con fuentes de corriente con inversor. Este sistema de soldadura corresponde básicamente al hardware de un sistema MIG/MAG de última generación, tomando en cuenta sin embargo ciertas condiciones específicas. Cabe mencionar especialmente el propulsor del alambre altamente dinámico, directamente dentro de la antorcha. La fuente de corriente, tan pronto percibe un corto circuito, inicia un movimiento retráctil del alambre de soldadura, reduciendo simultáneamente la corriente. Se desprende exactamente una gota, sin la menor salpicadura. Después corre el alambre otra vez hacia el frente, comenzando así un nuevo ciclo. Una frecuencia alta y una gran precisión, son las condiciones fundamentales para una transferencia de materiales absolutamente controlada. El propulsor del alambre dentro de la antorcha se concibió sólo para ser rápido, pero no para tener gran fuerza de tracción. La realimentación del alambre depende por tanto de otro impulsor principal más fuerte, pero que por lo mismo resulta más lento. Para compensar el movimiento de alta frecuencia del alambre, que se sobrepone al movimiento lineal, se utiliza un tampón en el ducto de alimentación.
Resumen
El proceso CMT representa un procedimiento de ensamblaje de acero con aluminio de fácil aplicación. Aparte de eso, el CMT presenta características mecánicas y tecnológicas más que satisfactorias. No sólo es de gran interés la unión de acero con aluminio, sino también es altamente atractiva una gran variedad de otras aplicaciones potenciales. Se cuentan entre éstas, la soldadura sin fusión de láminas recubiertas, así como la soldadura de láminas delgadas de aluminio o la soldadura de magnesio. Actualmente se están llevando a cabo numerosos experimentos. De los cuales se desprenderá, qué otras aplicaciones se podrán sumar al procedimiento CMT.
Carácter doble de la unión acero-aluminio.
Dosificación exacta de goteo y transferencia controlada mediante la retracción definida del alambre.
Fuente de corriente CMT, completamente equipada con impulsor de alambre CMT, antorcha CMT, tampón de alambre y sistema de enfriamiento.
Tampón para liberar al movimiento de avance progresivo de alimentación de alambre, de la oscilación proveniente de la parte frontal de la antorcha.
Antorcha de soldadura CMT durante la unión de lámina de acero con lámina de aluminio.
Cordón de soldadura a tope de dos láminas delgadas de aluminio.
Principio
La unión de materiales desiguales exige un conocimiento profundo de las propiedades de cada uno. Al aluminio se le aprecia sobre todo por su bajo peso específico, así como por sus características óptimas de aplicabilidad y procesamiento. Por otro lado, al acero, debido a su dureza y bajo costo, sería inimaginable dejar de usarlo en infinidad de campos. Otros aspectos necesarios y concretos son principalmente la resistencia a la corrosión, el coeficiente de expansión térmica, así como las propiedades atómicas. En la soldadura sin fusión, intensa en calor, de acero con aluminio, se produce una capa limítrofe entre ambos materiales conocida como fase intermetálica. Entre mayor sea la aportación térmica, más amplia será la fase intermetálica y más pobres serán las propiedades mecánicas de la unión. Asimismo, las características químicas y físicas exigen que se tomen medidas especiales. Los diferentes coeficientes de expansión de ambos materiales originan un campo de tensión en su zona de unión. No debe olvidarse la propensión marcadamente mayor a la corrosión. La causa de esto es el gran diferencial de potencia electroquímica del acero con respecto al aluminio. Todas las tecnologías que se han ocupado hasta ahora de la unión del acero con el aluminio, han sido realizables sólo con ciertas geometrías o únicamente con un gran despliegue de control técnico. A pesar de que muchos expertos en metalurgia consideraban la teoría de que la soldadura entre el acero y el aluminio no era viable, extensos trabajos de investigación con los procesos MIG/MAG demostraron que de hecho existía un potencial para la soldadura por arco eléctrico de estos materiales. El proceso CMT fue el resultado de una gradual adaptación de la soldadura MIG/MAG a los requerimientos del ensamble entre acero y aluminio. El CMT brinda una transferencia de materiales, controlable y casi sin emplear corriente. El material base de aluminio se funde junto con el material de aporte de aluminio, proceso en el cuál la masa fundida moja al material de acero galvanizado. El alambre de soldadura se mueve en intervalos rápidos en dirección contraria al avance. Esta retracción del alambre definida con precisión tiene el efecto de una dosificación controlada de las gotas, para lograr así una transferencia de materiales limpia y sin salpicaduras. El vaivén del alambre se realiza a una alta frecuencia y requiere un accionamiento altamente responsivo, sin engranajes, directamente en la antorcha. Obviamente la alimentación principal del alambre no puede seguirle el ritmo a este movimiento. Por tanto, el ducto de alimentación de alambre viene provisto con un tampón, el cual compensa el movimiento adicional hacia adelante y atrás del alambre.